Facilities
Wirco maintains a strong commitment to USA based manufacturing and our facilities are proudly located in the cities of Avilla, Indiana, Champaign, Illinois, and Wapuaca, Wisconsin. Our industrial footprint is comprised of five distinct sites each contributing to Wirco’s production output which helps to keep our production stream vertically integrated. All of Wirco’s facilities have seen large capital investments to keep them modern, efficient, and safe for our almost 200 dedicated employees.
Wirco Corporate Campus
Avilla, Indiana
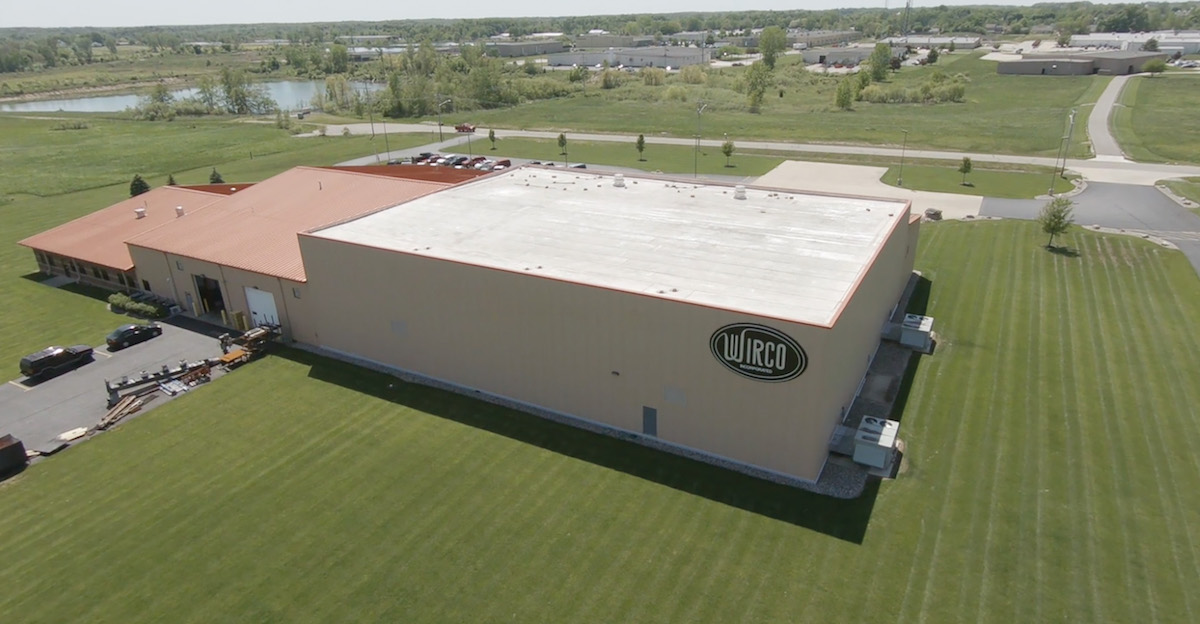
The centerpiece of Wirco’s Avilla manufacturing campus is the recently commissioned Wirco Global Headquarters Office and Manufacturing facility. In response to increased demand for our products, Wirco’s Strategic Planning Initiative determined the need for additional space for equipment, office staff, and warehousing. Purchased in 2015, along with an additional 10 acres of buildable land, the 47,000 sqft office and manufacturing space is located adjacent to Wirco’s other two Avilla manufacturing centers. The capabilities of Wirco Plant 3 were updated to include climate-controlled CNC milling and turning on over 20 pieces of equipment. Additionally, Plant 3 houses Wirco’s robotic orbital welding stations and final assembly booths to manufacture high-temperature cast radiant tubes, furnace rolls, and so many other custom heat and wear-resistant products along with Wirco’s heat treatment fan department and a greatly improved shipping/receiving area.
Wirco Plant 2 is home to both the manufacturing division of Hyper Alloys and the modern CNC pattern machining center for the Wirco Champaign Foundry. Fully renovated in 2016, Wirco Plant 2 has a fully climate-controlled space for tight-tolerant CNC machining, multiple welding stations, and press breaks for the manufacture of fabricated heat-resistant tooling and furnace parts.
Wirco's Plant 1 was built in 1984 as a top of the line fabrication facility, it features over 35,000 sqft of manufacturing space dedicated to the building of heat treatment tooling, baskets, and specialty fixtures. With a large modernization project completed in 2017, Wirco Plant 1 has over a dozen welding bays in addition to automated and manual pressure welding equipment. Our capabilities as a metal fabricator are supported by a variety of new or rebuilt metal working equipment stations. These include press brakes, rod coil straightening, metal sheers, metal rolls, saws, and over 40 different welding units of various styles. Plant 1 produces thousands of heat treatment baskets and fixtures yearly and continues to lead in quality and on-time delivery for our thermal processing customers.
Foundry Division
Champaign, Illinois
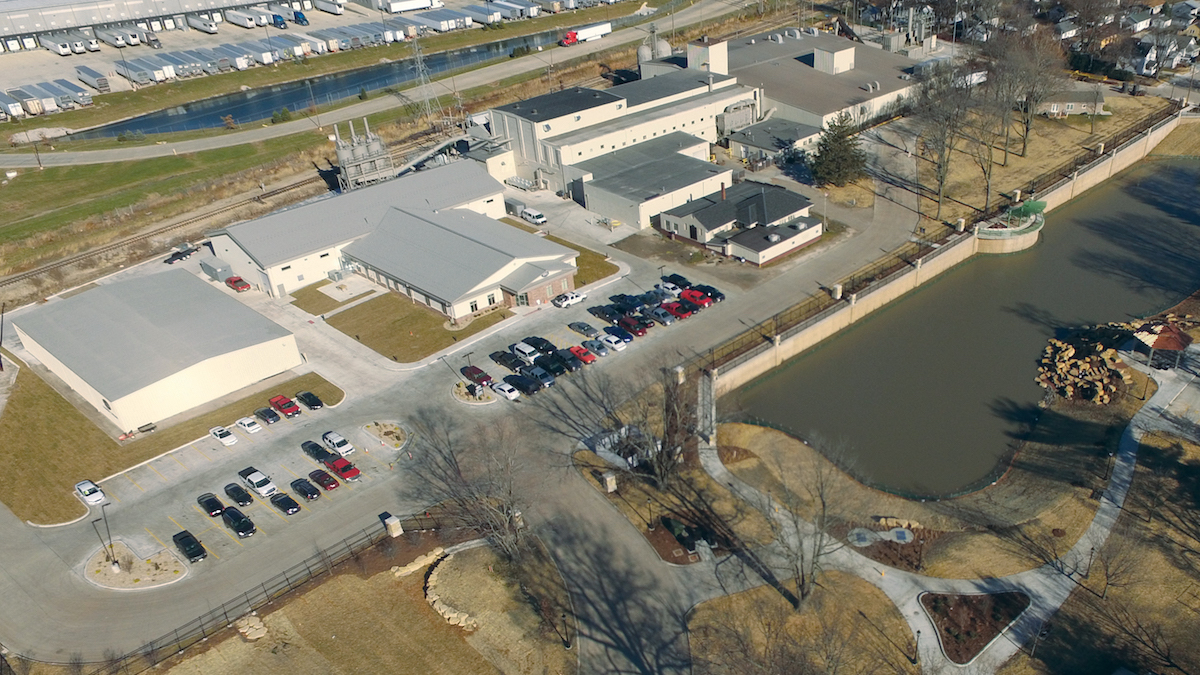
Since 1941, the foundry division of Wirco, Incorporated has been continually producing stainless steel castings at our newly renovated Champaign, Illinois foundry complex. The Wirco foundry has an established history of producing long-lasting alloy castings purchased by thousands of clients in North America and the larger global marketplace. Unlike other alloy foundries, the Wirco foundry focuses specifically on heat-resistant stainless steels, found primarily in tooling and furnace components utilized in the heat-treating and steel production industries.
With over 178,000 sqft, the Wirco foundry has the capacity and equipment needed to perform all the vertically integrated operations required in the production of both our static molded and centrifugally spun castings. To ensure quality castings, Wirco invests heavily in pre-casting operations, which include an experienced process-engineering department utilizing Magma-Flow simulation software, in-house CNC pattern making, and on-site core production. The foundry also houses a new metallurgical lab staffed by degreed metallurgists and numerous lab technicians who maintain Wirco’s metal integrity and A2LA lab accreditation.
To meet the needs of our ever-growing list of heat treatment, steel mill, and OEM customers, Wirco has upgraded or replaced all eight of our melting furnaces which are comprised of two arc furnaces and six induction melting furnaces. Along with this large melt capacity, Wirco operates seven distinct green sand molding systems in addition to a newly installed Tinker Omega No-Bake (Chemically Bonded Sand) molding line. Capable of producing hundreds of No-Bake molds per day with a diverse range of mold sizes, the Tinker molding line and adjacent thermal sand reclamation system offer the molding efficiency and quality Wirco customers trust. Complimenting Wirco’s static molding lines is our automated Duker centrifugal tube casting system. Wirco utilizes the Duker tube casting system to produce high-quality centrifugally cast tubing used in the production of radiant tubes, furnace rolls, and direct shipment tube bodies for Wirco’s OEM and fabrication clients.
Performance Industrial Products is a dynamic Wirco foundry specializing in sand and centrifugal castings. Out Waupaca division pours castings that range from ounces to 3,500 pounds in our recently modernized foundry space. The Waupaca foundry team casts in both stainless steel and steel alloys focusing on producing high-quality castings promptly at competitive prices.
We also offer Fabrication, Machining, and Heat Treating Alloys through our relationships with many highly qualified suppliers. The main industries we serve are heat treating, power generation, steel mills, farm and construction equipment, railroad, petrochemical, fluid, military, and furnace OEMs.